Dunbar II Subsea Pipeline
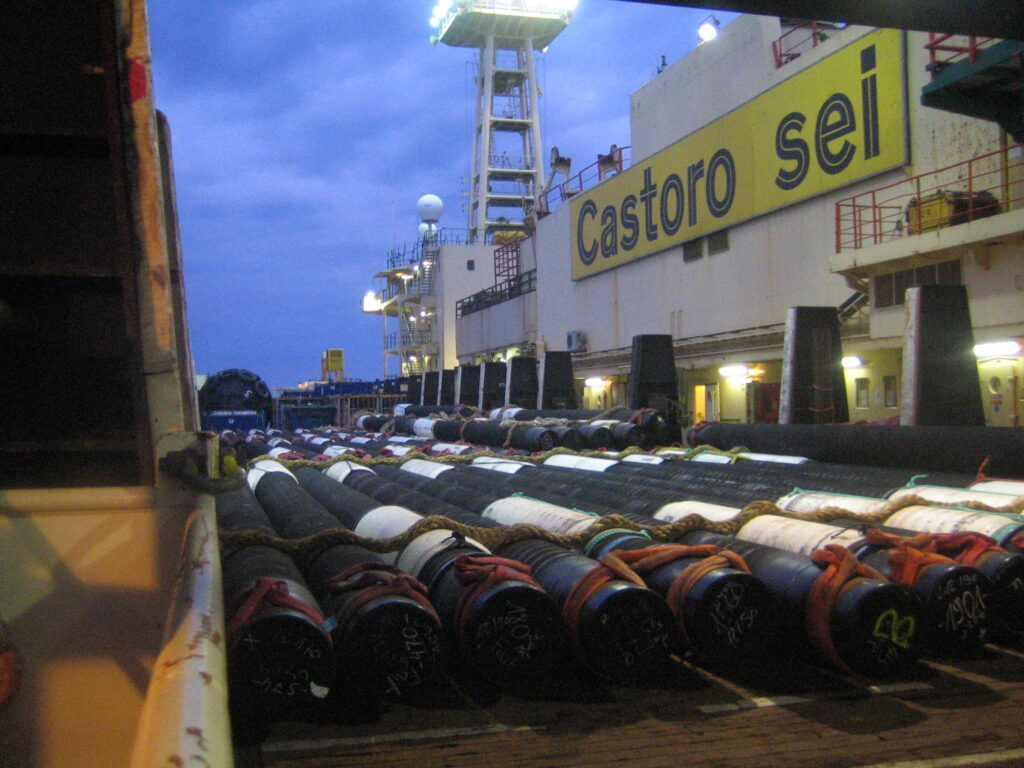
2 years
2007 – 2009
1st Use
CRA lined PiP
0,8W/².K
U-Value
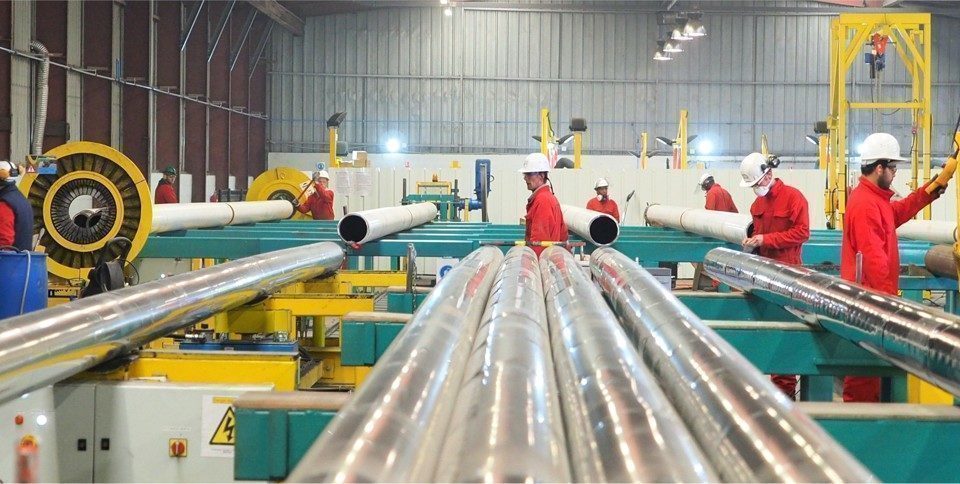
Quick Summary of Dunbar II Project
- Northern North Sea
- Client: Total Energies
- 2007
- 22 km, 16” / 18,6”
- CRA lined pipe
- 100°C
- U-value= 0,8W/².K
Our Challenge
The Dunbar Phase II project presented a critical task: replacing the original Dunbar pipe-in-pipe (PIP) system, which had been in operation since 1994. This system needed an upgrade to accommodate high-temperature flowlines operating at 100°C while mitigating risks such as lateral buckling over the 22 km subsea pipeline
Our Solution
To address the challenges of the Dunbar II project, ITP Interpipe implemented an innovative pipeline system with the following key features:
- High Performance: Utilized corrosion-resistant alloy (CRA) lined pipes to ensure durability and resistance to fluid constraints.
- Thermal Insulation: Achieved an efficient U-value of 0.8 W/m².K to maintain optimal temperature for high-temperature flowlines operating at 100°C.
- Lateral Buckling Mitigation: Employed a snake-lay installation method to handle thermal expansion and prevent lateral buckling in the 22 km pipeline.
- Advanced Installation: Adopted a single-joint S-lay swaged PIP system for rapid subsea installation.
- Efficiency and Reliability: Designed to replace and enhance the original Dunbar PIP system, extending the operational lifespan of the reservoir.
This solution ensured safe and efficient oil transportation under challenging subsea conditions.
Our Key to Success
The Dunbar II project succeeded through the use of advanced CRA-lined pipes, offering superior corrosion resistance and durability. The innovative snake-lay installation technique effectively mitigated lateral buckling, ensuring stability and reliability over the 22 km pipeline. Collaboration with Total Energies and a focus on achieving efficient thermal insulation allowed the system to perform optimally under challenging high-temperature conditions.