CRISP Subsea Bitumen Pipeline
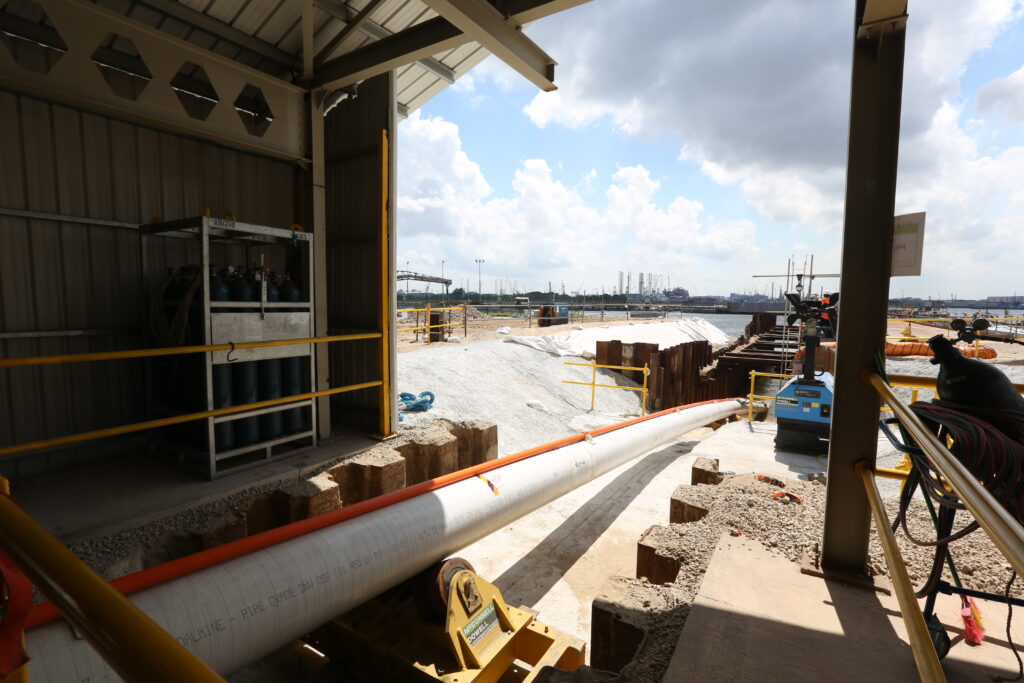
2 years
2018 – 2020
500,000
Manhours
228°C
Temperature
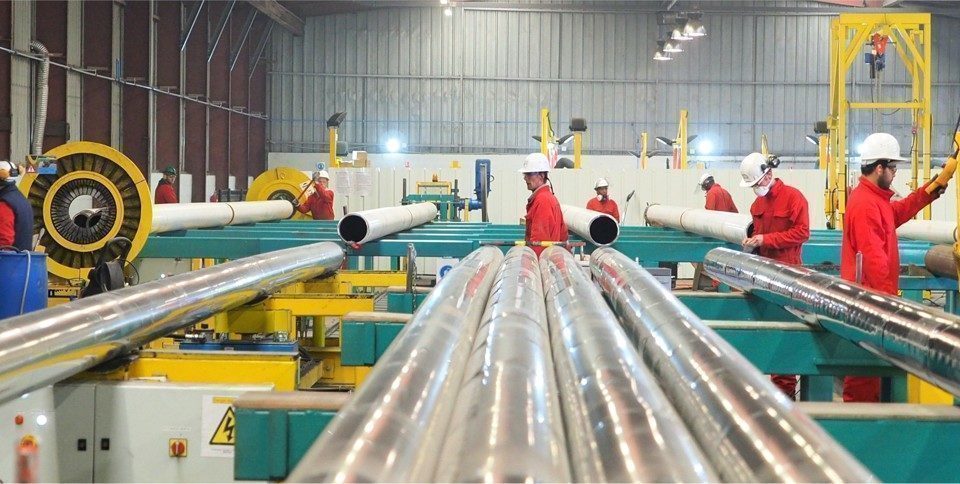
Quick Summary of CRISP Bitumen Pipeline project
- 228°C (460°F) design temperature – hottest subsea pipeline in the world
- 1,8 km subsea pipeline and 2 x 30 m onshore piping spools for bitumen transportation
- ITP’s Izoflex HT insulation providing a thermal performance (U-value)< 0.5W/m2-K
- 4 x 450 m pipe-in-pipe stalks and onshore piping spools
- Fiber optic technology: temperature sensing & pipeline integrity monitoring with annular pressure monitoring
- ITP’s Izoflex HT insulation providing a thermal performance (U-value)< 0.5W/m2-K
Challenge
The highly viscous bitumen has a minimum flowing temperature of 160°C. A U-value of 0.5W/m2-K is required to minimize temperature drop during operations and to extend cooldown times to for contingency shutdown procedures. An active heating system is needed for standard shutdown temperature maintenance and as a re-heat solution.
The high operating temperature exerts significant loading on the pipelines from thermal expansion, while space restriction at the landfalls mean that conventional expansion spools cannot be used.
Key to success
ITP experience with electrical heat tracing for subsea flowline applications was complemented by its in-house testing capability, which allowed proven concepts to be qualified to the project specification and constraints and confirm the design robustness during the project engineering phase.
The partnership with McConnell Dowell, a company with strong presence in Singapore, facilitated the timely obtention of all required regulatory approvals and ensured the selection of an optimum build and install philosophy.
Finally, a collaborative and transparent approach with ExxonMobil and a clear focus on quality and safety shared by all stakeholders enabled the overcoming of technical and execution challenges and secured the successful delivery of a highly innovative project.
Solution
The combination ITP’s Izoflex thermal insulation and AsphaltAx heat tracing technologies resulted in a system with less than 1°C temperature drop along the line and cooldown times above 45 hours, with indefinite temperature maintenance in shut-down and the capacity to re-heat.
Electrical heat tracing, temperature and pressure monitoring and pipeline integrity monitoring are handled by a standalone control & monitoring module delivered as part of the project scope. Fiber optic cables for temperature sensing and telecommunications purposes are also incorporated in the pipeline system.
The PIP design with strain coupling keeps the onshore footprint limited within the permitted area, with minimal end expansions.