CAMISEA LPG Pipeline
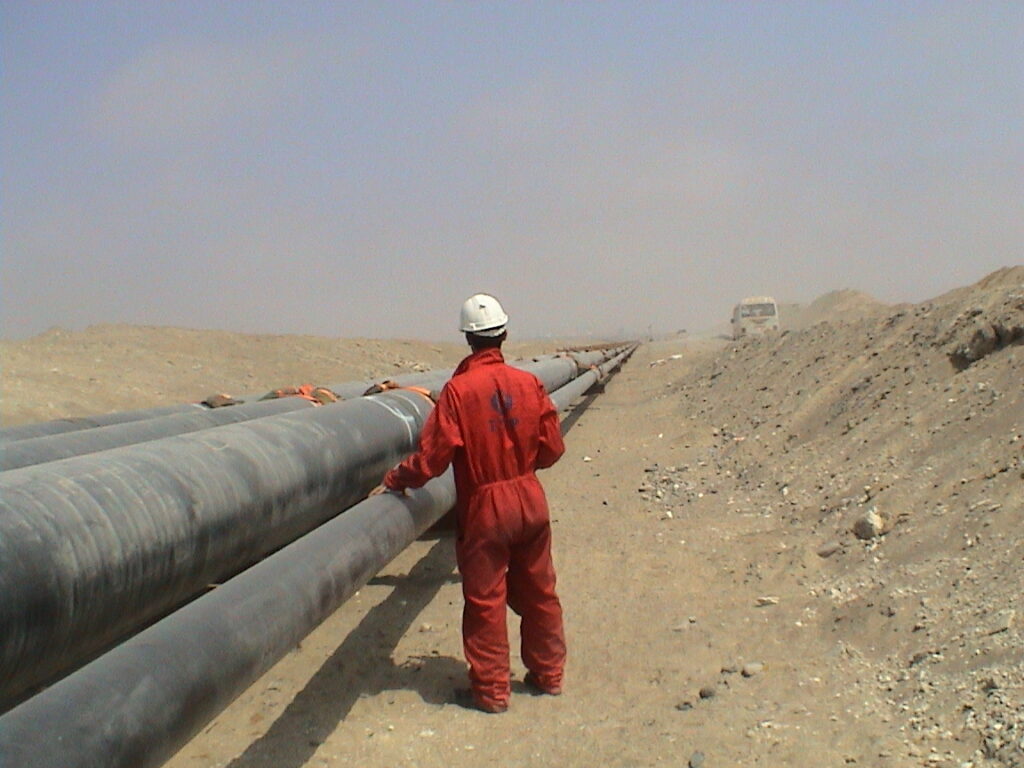
2 years
2002 – 2004
World 1st
Subsea Refrigerated PiP
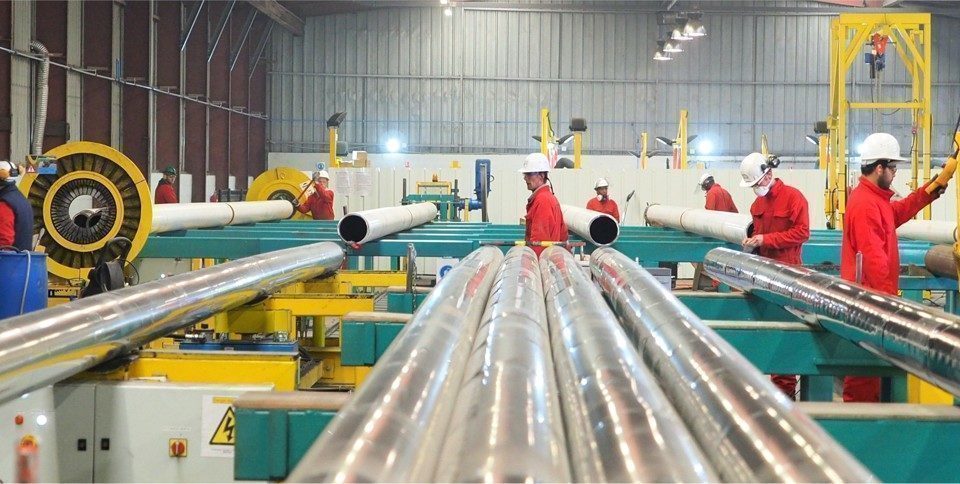
Quick Summary of Camisea LPG Project
- Pisco, Peru (250km South of Lima)
- Client: Pluspetrol
- Delivery system to offshore mooring berth
- Export of LPG, Naphta and Diesel
- Max Water Depth: 15m
- Flat-Pack Bundle 3170m long :
- 2 x 20”/24” Pipe-in-pipe
- 1 x 24” pipeline
- 1 x 10 ¾”
- 1 umbilical
- Design Temperature: -52°C
- U-value = 0.35 W/m²
- Extreme earthquake Design: 2007 magnitude 8 earthquake without damage
- Off-bottom tow and dredging installation
- 300 Tons Pull Winch
Our Challenge
Implement world first subsea LPG Pipeline to address project challenges, particularly related to environmental and logistical constraints. A conventional trestle, initially proposed for the offshore terminal, was not viable due to local objections related to visibility and interference with fishing routes. Additionally, there were concerns about collision risks and the high costs associated with the trestle structure.
Our Solution
ITP Interpipe developed a customized solution for the Camisea LPG project, addressing the unique challenges of Subsea LPG transport through several innovative design features:
- Jetty-less Design: In response to local concerns about visibility and interference with fishing routes, the subsea pipeline system was chosen over the traditional trestle. This approach eliminated collision risks and reduced costs, while minimizing environmental disruption.
- Limited Boil-Off and Thermal Efficiency: The pipeline system was engineered to continuously circulate product through cryogenic lines, maintaining low boil-off rates. This allowed for extended shut-in periods of over a week without compromising operational temperatures, optimizing energy efficiency and operational flexibility.
This integrated approach provided a safe, efficient, and sustainable solution for transporting LPG and other hydrocarbons in challenging offshore conditions.
Our Key to Success
The success of the Camisea LPG project lies in its innovative and cost-effective solutions. By opting for the subsea installation instead of a traditional trestle, the project minimized environmental disruption and maintained operational flexibility. Additionally, the project’s design was robust enough to withstand severe seismic events without compromising functionality, ensuring long-term sustainability and reliability.
World first subsea Refrigerated PiP operating since 2004
The facts are simple, the reason the facilities on and offshore courld resist this earthquake is a credit to AMEC Paragon and ITP. Because of this front-end planning and expertise, we could focus on emergency response and providing humanitarian aid to this area