ETAP Subsea Flowline

2 years
1998-1999
600
bar
1st
Izoflex utilization
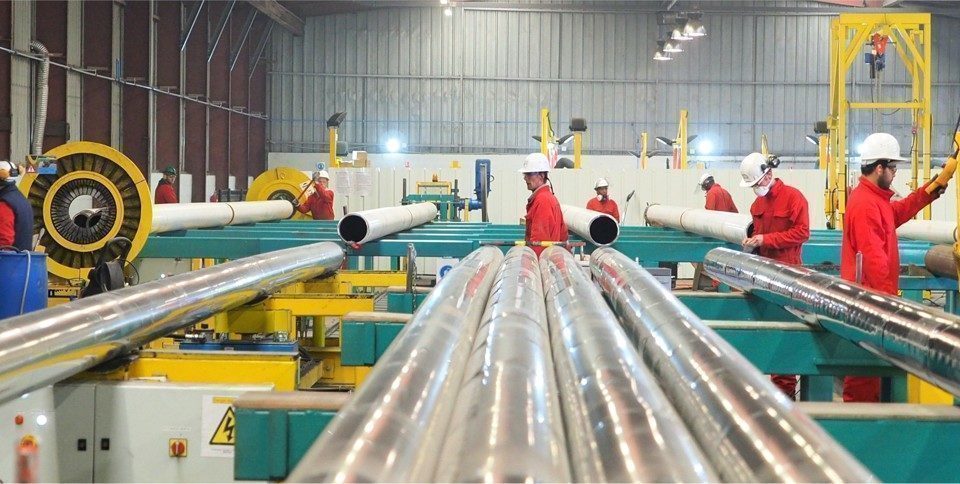
Quick Summary of Etap Project
- Central North Sea
- Client: Shell
- Operating since 1998
- Local content fabrication in Scotland
- 48 km, 12” / 16” PIP
- S-lay in 90 m water depth
Our Challenge
The ETAP project for Shell involved designing and installing a 48 km, 12″/16″ pipe-in-pipe (PIP) system operating in 90 m water depth. Therefore, the high-pressure (600 bar) and high-temperature (155°C) conditions required a custom solution that could handle thermal expansion, transients, and fatigue. Additionally, the insulation needed to meet stringent performance criteria while maintaining a compact design.
Our Solution
ITP developed a tailored solution for the ETAP project, incorporating several key features to address the high-pressure (600 bar) and high-temperature (155°C) challenges:
- Compact Design: The system was designed to be compact while meeting Shell’s insulation requirements, utilizing Izoflex pipeline insulation to achieve a U-value of 1.2 W/m².K, optimizing space without compromising thermal performance.
- Tulip Inserts for Strain Coupling: The custom tulip insert design was incorporated to ensure distributed strain coupling, effectively managing thermal expansion and transient loads throughout the pipeline.
- Field Jointing for HP/HT: Advanced field jointing techniques, including full-penetration outer pipe welding, were used to ensure the integrity of the pipeline and enable the system to handle the extreme thermal expansion and fatigue demands of the HP/HT environment.
- Local Fabrication: The system was fabricated in Scotland, ensuring high-quality manufacturing with a focus on local content and expertise.
This integrated approach provided a reliable, high-performance pipeline solution for Shell’s demanding offshore field.
As a result, this solution ensured safe and efficient oil transportation under challenging subsea conditions.
Our Key to success
The project’s success stemmed from innovative engineering solutions, including the use of Izoflex insulation and a robust welding approach that met Shell’s high standards. Moreover, the custom tulip design ensured effective strain management and enhanced system reliability under extreme HP/HT conditions. Collaboration with Shell and adherence to stringent insulation and performance requirements further ensured the pipeline’s performance.